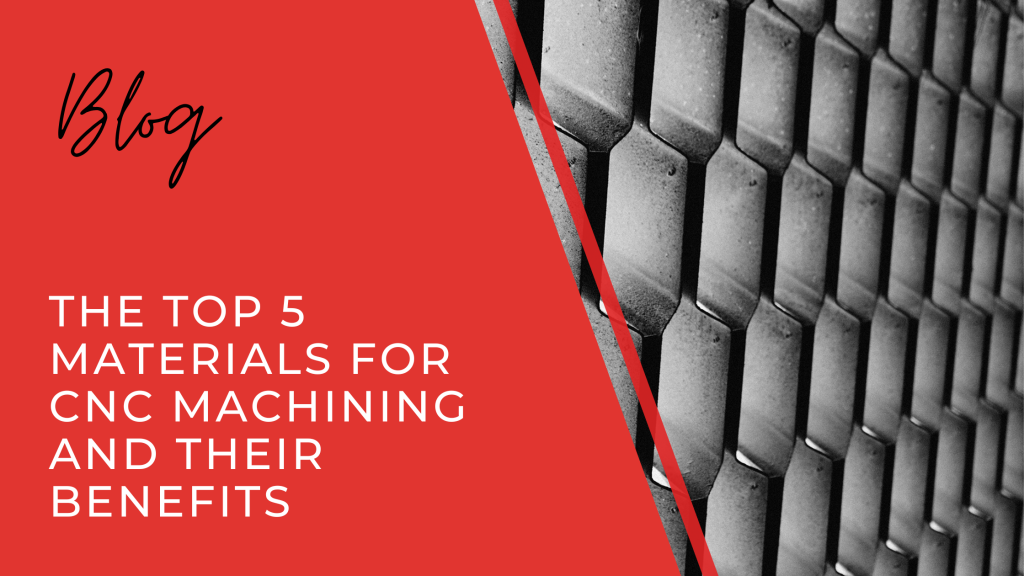
When it comes to CNC machining, material selection is key to the success of any project, big or small. Whether you’re building prototypes, high-precision parts, or large-scale production runs, choosing the right material can be the difference between a perfect fit and a costly misstep. Here’s a breakdown of the top five materials commonly used in CNC machining, along with their advantages and disadvantages so you can ensure the right materials are used for your project.
1. Aluminum
Aluminum is one of the most versatile and widely used materials in CNC machining. It’s light, strong, and corrosion-resistant, making it suitable for a variety of industries.
Pros:
Lightweight and durable: Perfect for aerospace, automotive, and consumer products.
Corrosion-resistant: A great choice for outdoor or marine applications.
Highly machinable: Results in faster production times and lower costs.
Cons:
Not the strongest: For projects requiring extreme strength or heat resistance, aluminum might fall short.
Limited welding ability: Certain aluminum alloys can be difficult to weld.
2. Stainless Steel
Known for its toughness and resistance to corrosion, stainless steel is a popular material for high-stress applications.
Pros:
High strength: Ideal for parts that need to endure stress and wear.
Corrosion-resistant: Withstands harsh environments like marine and chemical industries.
Diverse grades: Various alloys, like 304 and 316, offer specific properties for different needs.
Cons:
Harder to machine: Slower speeds and more tool wear can drive up costs.
Heavier than alternatives: Not suitable for projects where weight is a concern.
3. Brass
Brass is a favorite for parts requiring excellent electrical conductivity and low friction.
Pros:
Easy to machine: Brass has one of the highest machinability ratings.
Corrosion-resistant: Performs well in plumbing, electrical, and decorative applications.
Low friction: Ideal for gears, locks, and applications requiring smooth motion.
Cons:
More expensive: Brass tends to be pricier compared to other metals like aluminum and steel.
Not as strong: It lacks the strength needed for high-stress environments.
4. Titanium
Titanium offers an excellent balance of strength, weight, and corrosion resistance, making it a go-to material in the medical, aerospace, and automotive industries.
Pros:
High strength-to-weight ratio: Nearly as strong as steel but much lighter.
Biocompatible: Perfect for medical implants and devices.
Corrosion-resistant: Performs well in extreme environments, from deep-sea exploration to space.
Cons:
Costly: Titanium is significantly more expensive than other metals.
Difficult to machine: Requires specialized tools and techniques, adding to production time and cost.
5. Plastics
When weight, flexibility, or cost is a concern, plastics can be an excellent option for CNC machining, with a wide variety of types available for different applications.
Pros:
Lightweight and affordable: Commonly used for consumer goods, electronics, and packaging.
Versatile: Options like nylon, PEEK, and polycarbonate offer unique properties like chemical resistance or thermal stability.
Easy to machine: Often results in faster production times with less wear on tools.
Cons:
Lower strength: Plastics can’t compete with metals in terms of tensile strength or durability.
Heat sensitivity: Some plastics may deform under high temperatures, limiting their use in high-heat environments.
Each material offers its own unique blend of properties, making it crucial to match the right material with the demands of your project. By carefully considering the pros and cons of each material, you can ensure that your CNC machining project is both efficient and effective. Looking for precision CNC machining that exceeds expectations? Call us at (262) 347-2004 or email sales@unitedtoolllc.com to schedule a tour of our state-of-the-art facility. Discover how we can streamline your manufacturing process and deliver superior value.