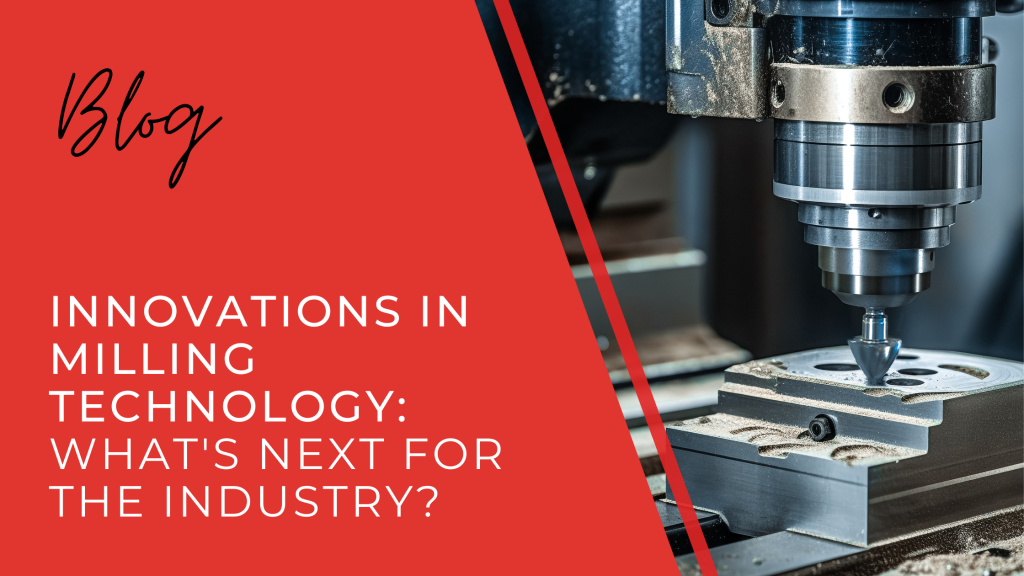
Like everything in life, the manufacturing industry is constantly evolving, with technological advancements driving efficiency, productivity, and innovation. Milling technology, a cornerstone of manufacturing, has seen significant changes over the years and will only continue to develop in the coming years. Here are a couple things we can expect in the future.
Enhanced Software Accessibility
In the past, one of the main roadblocks to adopting advanced milling technology was the complexity of the software required to operate CNC (Computer Numerical Control) machines. This software was often difficult to learn and required extensive training, making it less accessible to smaller operations.
That has all changed, software developers have made significant measures in improving user-friendliness. Modern CNC software is designed to be intuitive and accessible, reducing the learning curve and enabling more businesses to adopt these advanced machines. This trend is expected to continue, with software becoming even more streamlined and integrated with other digital tools.
The Rise of Multi-Axis Milling Machines
The number of axes a milling machine can operate on significantly impacts its versatility and efficiency. Traditional milling machines typically operate on three axes, but modern advancements have introduced 5-axis and even 6-axis machines.
What does this mean? These multi-axis machines can perform more complex cuts and reduce the need for manual repositioning of the workpiece, leading to increased precision and reduced production times. As technology continues to advance, we can expect to see even more sophisticated multi-axis machines that offer unparalleled flexibility and productivity.
Increased Computational Power
The computational power of CNC machines is another area where we will see BIG advancements. Modern CNC machines are equipped with powerful processors that can handle complex calculations quickly, improving the speed and efficiency of the milling process.
Additionally, AI isn’t going anywhere anytime soon, and advancements in AI and machine learning are beginning to be integrated into milling technology. These technologies can predict potential issues before they occur, optimize tool paths, and improve overall machine performance. As AI continues to evolve, its role in milling technology is expected to grow, leading to smarter and more efficient manufacturing processes.
Material Adaptability and Versatility
One of the most exciting trends in milling technology is the increased adaptability to different materials. Traditionally, milling machines were primarily used for metalworking. However, modern machines can handle a wide range of materials, including plastics, composites, and even ceramics.
This versatility opens up new possibilities for manufacturers, allowing them to produce a broader range of products and respond more quickly to market demands. As material science advances, we can expect milling technology to adapt further, providing even greater flexibility and efficiency.
Integration with Additive Manufacturing
Additive manufacturing, or 3D printing, has been a disruptive force in the manufacturing industry. Rather than viewing this technology as a competitor, many manufacturers are finding ways to integrate additive manufacturing with traditional milling processes.
Hybrid machines that combine additive and subtractive manufacturing techniques are becoming more common. These machines offer the best of both worlds, providing the precision and reliability of milling with the flexibility and creativity of 3D printing. This trend is likely to continue, leading to new manufacturing possibilities and more efficient production methods.
Sustainability and Energy Efficiency
As with many industries, sustainability is becoming a big consideration in manufacturing. Milling technology is evolving to become more energy-efficient and environmentally friendly. This includes advancements in machine design, such as improved lubrication systems, energy-efficient motors, and better waste management processes.
Digital tools that optimize machining processes can significantly reduce material waste and energy consumption. As sustainability becomes an increasingly important factor, we can expect to see continued innovation in this area, helping manufacturers reduce their environmental footprint while maintaining high levels of productivity.
As you can see, the future of milling technology is bright, with numerous exciting advancements on the horizon. At United Tool, we are committed to staying at the forefront of these developments, ensuring that our clients have access to the latest and most efficient milling solutions. Discover precision and quality at United Tool—visit our facility today or call (262) 347-2004 to schedule a tour!